Lubricants are the lifeblood of meat and poultry processing machinery.
Keeping equipment properly lubricated is vital if plant operators are to maximize the life of technologies and enjoy optimal output with limited downtime. Analysts say the best way to do this is by implementing a strict lubrication regimen.
“It is essential that meat and poultry processors lubricate such equipment as motors, pumps, gear cases and conveyor belts with food-grade greases,” says Bryan Johnson, board chairman of the Broken Arrow, Okla.-based International Council for Machinery Lubrication (ICML). “Most important is leveraging lubricants with a viscosity that ensures separation of the lubricated surfaces, such as gear teeth, while minimizing energy requirements to operate the machine. Users should consider additives that reduce wear and extend the oxidative resistance of the lubricant.”
That is vital as the harsh meat and poultry processing environment can be detrimental to the integrity and performance of lubricants, Johnson says. “Cleaning water can enter into the machine internals and mix into the lubricant,” he says. “It can have immediate catastrophic consequences or become a hidden latent stressor to both the lubricant and the lubricated machine surfaces by causing corrosion or impacting the viscosity of the lubricant.” In addition, airborne contaminants can degrade the cleanliness of the lubricant, with the dirty grease increasing wear rates within machines, Johnson says.
Keep the seals in sight
The erosion of seals that help maintain lubricants in equipment, meanwhile, can cause gearbox and hydraulic system leaks, says Norman Marriott, emeritus professor in the College of Agriculture and Life Sciences at Virginia Polytechnic Institute and State University (Virginia Tech) in Blacksburg. Ensuring seals are strong enough to prevent grease from leaking is crucial because the lubricants also can alter the effectiveness and appearance of equipment and protein products, he says. In addition to typical wear and tear, workers can damage seals when using very high-pressure water for cleaning, Marriott says.
A combination of effective lubrication and machine maintenance, meanwhile, will help lower the likelihood of equipment problems, Johnson says. “The proper selection of seals and gaskets can reduce the ingress of water and other contaminants and the installation of breathers to the equipment also can help,” he says. Desiccant breathers prevent the entry of such contaminants as moisture, and dirt and debris particles, into machinery, which can adulterate the lubricant and damage the equipment over time.
Processors can better maintain machinery by setting schedules for measuring and replacing lubricants and analyzing seal integrity, Johnson says, along with the ongoing laboratory testing of lubricant quality. While plant workers should typically lubricate machinery at least once a day, and preferably following a production shift, excess leakage may demand more frequent applications, Marriott says.
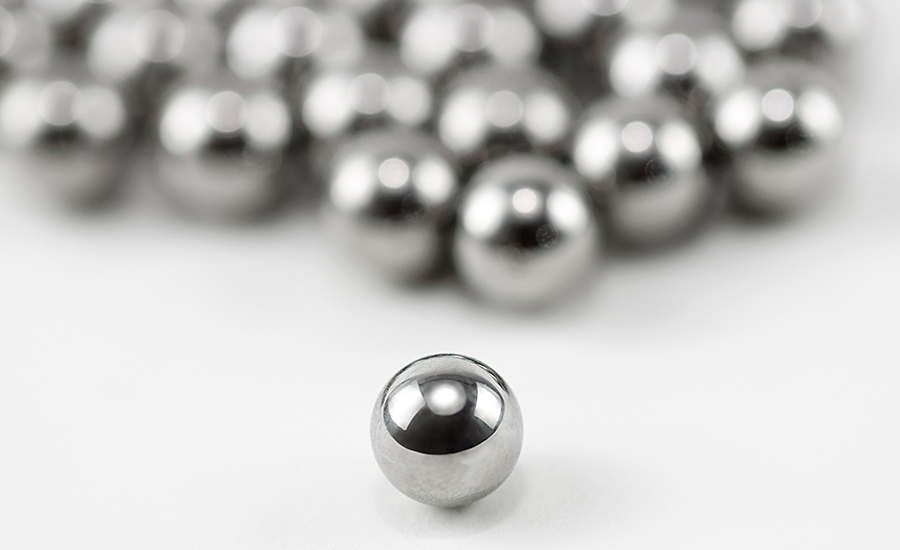
Stay on track with training
The most effective meat and poultry processing facilities have highly trained and certified in-house staff who can follow proper lubrication practices and identify when facilities require outside expertise, Johnson says, noting that ICML maintains a listing of upcoming training events and offers independent certification of lubrication professionals based on the individuals’ training.
Supervisors, meanwhile, should be vigilant about ensuring that workers are following the correct lubricating procedures, Marriott says. “The most effective approach is on-the-job training with employees taught how to detect if a seal is leaking and the action to take if they observe leakage during a shift,” he says. “That might result in replacing the seal during break time or at the end of the day so production does not have to stop for the repair.”
In addition to incorporating more stringent maintenance techniques, processors can benefit from the availability of more robust lubricants, Marriott states. He says recent upgrades include formulas that make greases effective longer. Factors triggering formulation changes include stricter government regulations and the availability of chemical building blocks, Johnson says.
Processors should consult with the major lubricant suppliers to determine the most appropriate selections for their operations, says John Crossan, a Chicago-area maintenance manufacturing consultant. “The lubricant manufacturers are the most up to date on the latest improvements and will usually provide a survey at no charge if the customer will consider purchasing from them,” he says. NP