Grote Co., Stäubli Corp., PMMI, Beckham Automation, Grazr, and JLS Automation all share their current insights and anticipations for the robotics and automation industries.
Grote Co. is a food processing equipment manufacturer that offers a variety of systems for processors.
Stäubli Corp. is another player in the food automation sector, backing itself on its hygienic models.
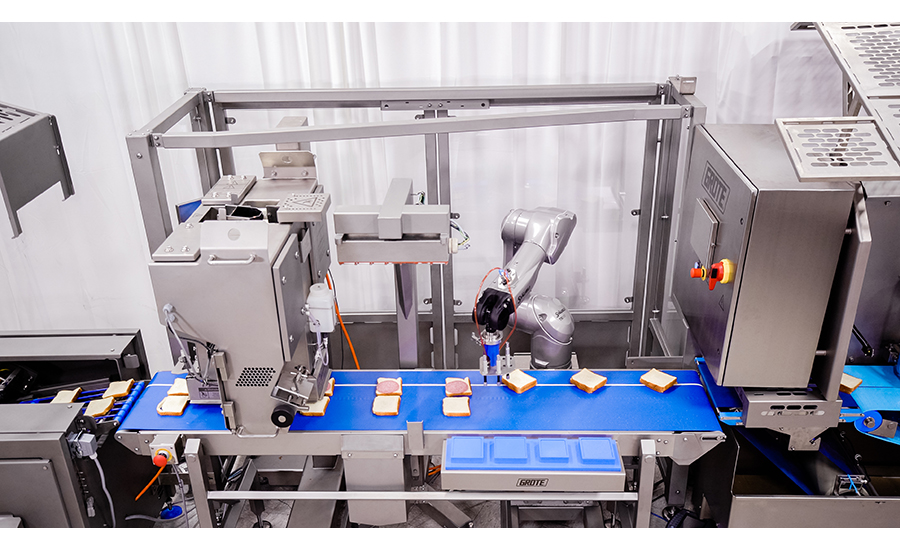
Many of these companies offer a variety of support options for their customers following installation of these automated systems. “The best support for our customer is our customer,” said Craig Souser, president and CEO of JLS Automation. By training workers, JLS works to ensure their customers are fully equipped to understand and utilize these automation systems.
Getting into automation
Within the last five years, especially in light of the recent pandemic, John Burke, regional sales manager for Stäubli Corp., has observed an increase in the demand for robotic automation in the meat industry. “What’s interesting is a lot of companies have some sort of automation in their plants … robotic automation is fairly new to the primary meat space,” said Burke. He noted that automation is not functioning to replace workers, but rather opens up the potential to shift the worker to a different position.
Souser cited repetitive motion as a reason his customers at JLS seek out robotic automation.
For smaller meat or poultry processors looking to begin automating some processing, Anthony Laney, CTO and co-founder of Grazr, an online market for local meats, recommended thinking about regulatory requirements, as well as integration capabilities for those seeking to implement software automation. He also recommended having ample training for any automation systems.
To ensure cybersecurity with automation systems, Laney advised processors to secure their data, as well as hardware, to adequately train workers — which includes cybersecurity training — and to regularly maintain their systems.
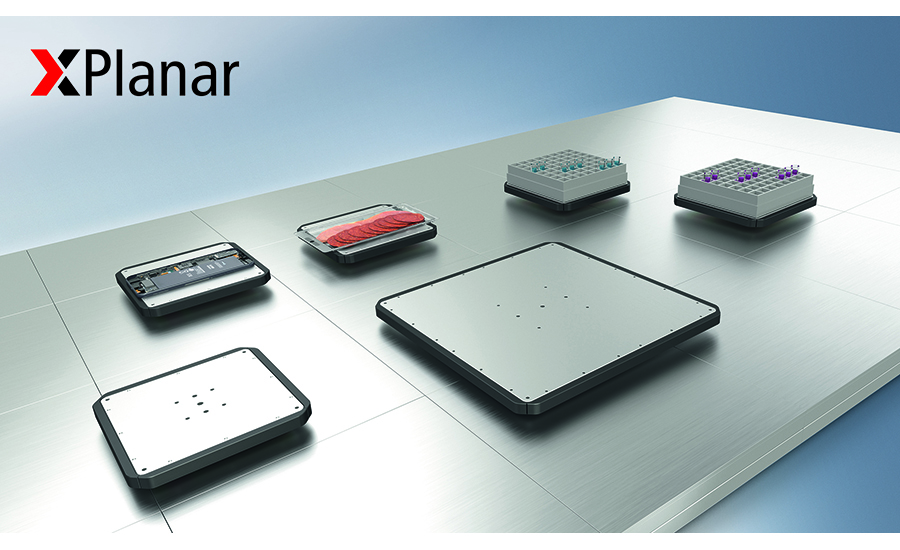
In the article “Automation overcomes workforce and productivity shortfalls,” Jorge Izquierdo, vice president of market development for PMMI, noted the problem that specialized training can cause in setting up automation systems. “This can be achieved by graphical operator interfaces, programmed to provide step-by-step instructions, thereby eliminating the need for specialized knowledge, advanced degrees, or programming skills,” he said.
Companies may face other challenges in the process of installing automation systems, including the setup of the building, finding suitable automation systems for certain processes, as well as investment cost, Izquierdo said. “Other challenges involve supply chain delays and long lead times; internal shortfalls (time, skills, budget); calculating the total cost of ownership (TCO); and scheduling downtime and resources for equipment implementation, training, and performance testing,” he said.
In his article, Izquierdo discussed robotics in the CPG industry. He anticipates growth potential for cobots. “Improvements in functionality such as vision, self-learning, and artificial intelligence will spur adoption,” he said. “Increasingly, cobots are viewed as the solution to the need for flexibility on the production line.”
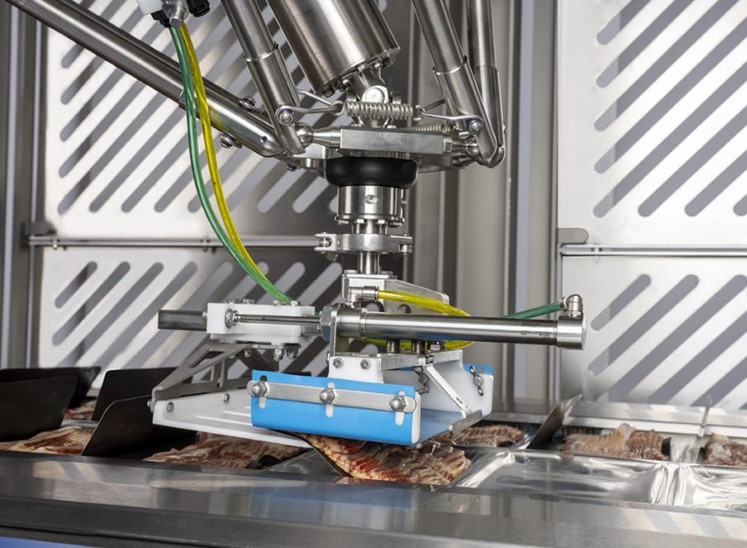
Izquierdo said that advancements in cobots are increasingly trending in popularity. “Comparatively inexpensive, modular, and adaptable, today’s cobots can be a perfect fit for smaller enterprises with low budgets,” he said.
He reported great potential for the robotics industry within CPG brands. “Three out of five CPG companies using robotics plan to increase installations during the next five years, particularly for secondary and transport packaging applications,” Izquierdo said.
Mark Ruberg, packaging industry manager for Beckhoff Automation LLC, sees the demand for automation in CPG as well, particularly noting the demand for customization. “Changing consumer demands and e-commerce are driving this trend. However, traditional control, conveyance, and rigid robotics options aren’t keeping pace,” Ruberg said. “Advanced mechatronics technologies like XTS and XPlanar create a completely new machine design toolkit for engineers.”
Beckhoff Automation is a supplier that offers automation in various industries.
Business benefits
Laney said integrating automation processes can improve quality of products, efficiency, traceability, management of inventory, and worker safety. He also said they can reduce waste.
Regarding business development, Laney noted that automation systems can allow processors a higher level of flexibility. “For example, an automated system can be quickly reprogrammed to handle a new type of product or packaging format, allowing processors to expand their product lines and meet customer demands,” he said.
The systems can also allow for deeper insight into the company’s data analytics, he said.
Shane Peterson, key account manager at PFI, a Grote Co. brand, said vision technology can help with quality control.
“Vision can handle variability in different cuts and portions to help maintain a consistent size or weight on each line, as well as new track and trace concepts,” Ruberg said. “But there are other ways to decrease waste beyond upgrades. Two major trends are optimizing data acquisition and the operator interface.
Looking at software, Ruberg sees the value of HMI. “This cuts down on training for new operators,” Ruberg said. “Secure remote access for the OEM is valuable, but empowering operators or maintenance to quickly resolve issues via the HMI is even better,” he said.
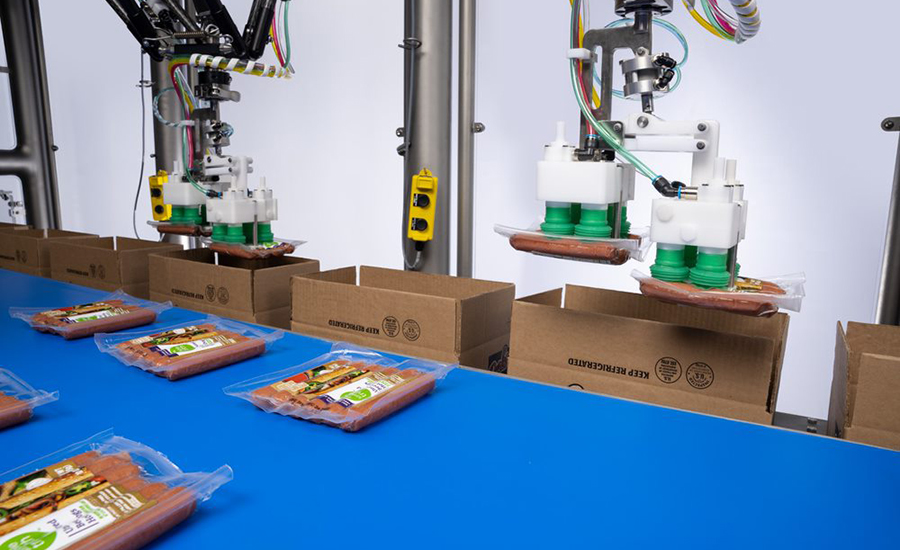
Ruberg also noted the benefits of automation regarding sourcing challenges. “In terms of sourcing components, choosing open platforms and technologies can be a competitive advantage,” he said.
“Automation systems mesh well with processors' efforts to maximize efficiency and improve the bottom line,” said Danny Friend, Lifecycle Leader at Grote Co. He said uptime is a draw for automation systems.
Friend said that humans will always be necessary in a processing environment. Still, he observed the clear benefits of automation systems. “With the continued advancement of robotics and AI technologies, many opportunities exist to streamline and enhance reliability in food production environments,” he said. “We believe this trend will yield positive returns on investment, making it an excellent business solution now and in the future.”
Safety
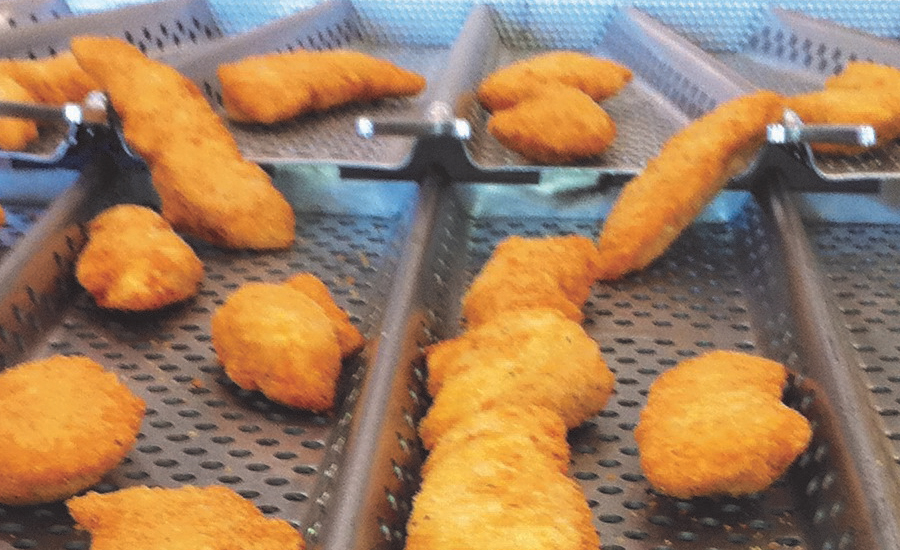
Not only does automation decrease the risks of human contamination, but it also can diminish risk for human error, according to Laney. Automation can also expand shelf life capabilities. “Automation can help extend the shelf life of meat and poultry products by reducing the risk of contamination and spoilage,” Laney said.
“In many cases, a food processing packaging line is a big buffet, especially if you’re dealing with uncooked products, RTE for sure,” Souser said. He said that food safety is a huge force in automation.
In addition to diminishing germs from human workers, automation systems also provide traceability benefits, Burke said.
Automation systems not only benefit food safety, but worker safety, as well. By protecting their workers more, companies can save more money they might have lost due to injuries, Peterson said. “Repetitive motion for a human can cause health-related issues over time,” he said.
Burke noted that automation also protects workers by removing them from potentially hazardous occupations, which then opens up the potential to move the worker to a different position.
Ruberg discussed zone-specific safety in automation systems. “Integrated machine safety, like Beckhoff’s TwinSAFE system, allows engineers to establish zoned safety. This means you can stop a specific section of a machine if triggered … without stopping the downstream process,” he said. “Only the affected area goes into a stopped, safe state. This can create significant benefits with throughput.”
Labor challenges and looking forward
A large draw to robotic automation is the alleviation of labor challenges. As the industry currently faces labor issues, automation systems can benefit operations.
Burke noted the necessity of automation systems. “Right now … we’re in a labor shortage. I do not see that ending any time soon. If you want to produce product, you will have to automate,” he said.
“You’ll have to figure out how to jump into this space if you haven’t already. That’s number one,” Burke said. “Number two is I just see the industry as a whole embracing automation more.”
Moving forward, Souser sees innovation in the category for both vision and AI.
Report Abusive Comment